Commercial Air Quality Testing
Commercial air quality testing is essential for maintaining a safe and healthy indoor environment. It is important for office buildings and other commercial spaces.
Testing helps identify contaminants that could affect the health and comfort of employees. This includes pollutants like dust, mold, and chemicals.
A thorough air quality test evaluates several factors. These can include ventilation effectiveness, humidity levels, and the presence of volatile organic compounds (VOCs).
Benefits of Air Quality Testing:
- Health and Safety: Reduces risks of respiratory issues and other health problems.
- Productivity: Improves employee performance by ensuring a comfortable work environment.
- Reputation: Shows commitment to employee well-being, which can enhance company image.
Indoor air quality is crucial in commercial buildings. Poor air quality can lead to issues like headaches, fatigue, and concentration problems.
Testing helps to meet standards such as the ASHRAE 62.1, which provides guidelines for proper ventilation to ensure acceptable air quality.
Regular air quality testing is a proactive measure. It can spot problems early, making it easier to address them before they become serious. This ensures a safe, healthy, and productive workplace.
Key Pollutants and Testing Procedures
Understanding the types of pollutants common in commercial settings and the methods used to test for and monitor these pollutants is essential for maintaining a healthy indoor environment.
Common Pollutants in Commercial Settings
In commercial settings, pollutants can originate from various sources and can impact indoor air quality significantly. Carbon dioxide (CO₂) levels can indicate the adequacy of ventilation. High levels may suggest insufficient air exchange.
Volatile organic compounds (VOCs), found in products like paints and cleaning supplies, can cause headaches and dizziness. Mold spores, resulting from poor moisture control, can cause respiratory issues and allergies. Similarly, dust and particulate matter (PM), which includes tiny particles like dirt and pollen, can aggravate asthma and other respiratory conditions.
Carbon monoxide (CO) is another serious pollutant. It’s a colorless, odorless gas that can be fatal at high concentrations. Allergens from plants, animals, and insects also contribute to poor indoor air quality in commercial environments.
Testing and Monitoring Techniques
Testing and monitoring indoor air quality in commercial settings involve several techniques. Air samples are taken to detect the presence and concentration of various pollutants. These can be collected using monitoring equipment such as portable air quality monitors or more complex sampling devices for laboratory analysis.
Measurements of temperature and humidity are important as they affect the indoor environment and comfort levels. Constant monitoring ensures these parameters remain within recommended ranges. Routine testing by certified industrial hygienists includes checking for specific pollutants like CO, VOCs, and particulate matter.
Some techniques involve ventilation studies to assess if there is adequate airflow throughout the building. Monitoring for mold and ensuring moisture control helps in preventing mold growth and related health issues. Utilizing these various techniques can help in maintaining a safe and healthy workplace, thereby protecting employee health and productivity.
Regulations and Remediation Strategies
Regulations for commercial air quality testing are critical to maintaining a healthy environment in business settings. OSHA compliance is key for ensuring safety in workplaces. Property managers must be aware of industry standards to address issues effectively.
Environmental consultants play a vital role in this process. They assess air quality and advise on best practices. This includes dealing with toxins, mold, and other pollutants.
Building materials can release harmful substances. Remediation involves replacing or treating these materials. Restoration contractors handle water damage, fire damage, and mold remediation to restore safe conditions.
Commercial buildings often require detailed guidelines for remediation solutions. These guidelines help to eliminate toxins and ensure proper air quality. ASHRAE Standards 62.1 and 62.2 provide important ventilation requirements.
Mold remediation is a common issue. To prevent mold growth, moisture levels must be managed. Rapid response to water damage is crucial. The EPA’s guidelines suggest fixing moisture problems within 48 hours.
Heating, ventilation, and air conditioning (HVAC) systems also need regular checks. Proper maintenance can prevent many air quality issues. HVAC systems should meet specific regulations to ensure they don’t contribute to air pollution.
Industrial settings have unique challenges. Contaminants from machinery and processes can affect air quality. Businesses must follow specific guidelines to manage these risks.
Commercial property managers must be proactive in addressing air quality concerns. Regular inspections and adherence to regulations will help maintain a safe environment for all building occupants.
[trustindex no-registration=google]
How can we help you today?
Our team is standing by and ready to help.
Text To Request Service Schedule Today: (281) 898-3773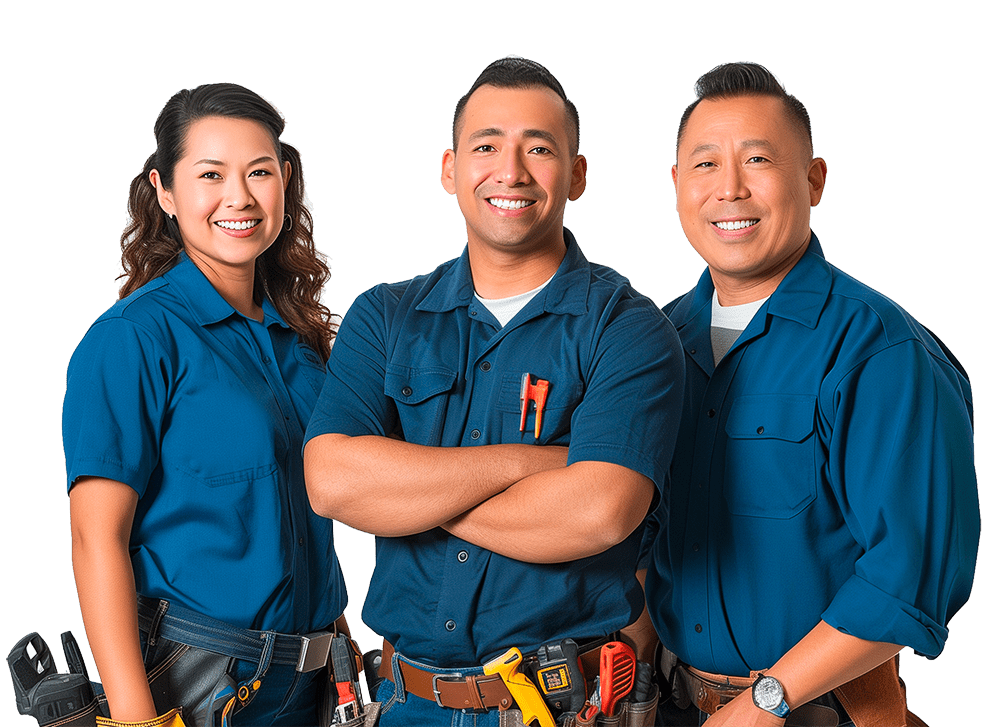